آبکاری الکترولس نیکل – فسفر و تاثیر آنها بر روی کارایی این پوشش ها در صنعت نفت و گاز(بخش اول)
چسبندگی پوشش
معمولا چسبندگی آبکاری الکترولس نیکل به فولاد های کربنی عالی است – نیروی چسبندگی این پوشش به فلز پایه معمولا بیشتر از 140 مگاپاسکال می باشد. لازم است برای بررسی چسبندگی پوشش های الکترولس نیکل – فسفر بر روی سطح آزمایش های دقیق انجام شود البته بیشتر آزمون ها کیفی و مقایسه ای هستند و به شکل و کاربرد قطعه بستگی دارند. زمان های که امکان انجام تست بر روی قطعه اصلی انجام نمی شود توصیه میشود که همراه با قطعه کار یک نمونه آبکاری الکترولس شود و بر روی آن تست انجام شود.
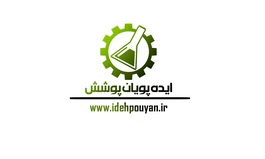
تخلخل پوشش
پوشش های نیکل فسفر می بایست بدون هیچ تخلخلی باشند تا حداکثر مقاومت به خوردگی را داشته باشند. معمولا خوردگی در داخل حفره ها شروع می شود این مساله جدی می شود زمانی که فلز پایه نسبت به الکترولس نیکل آندیک باشد (خودرگی گالوانیک). در نتیجه باید این مساله کنترل و آزمایش شود یک روش برای ارزیابی پوشش روش فروکسیل می باشد. (ASTM B689)
سختی
سختی پوشش های الکترولس نیکل را می توان با روش استاندارد ASTM B578 اندازه گیری کرد. نکته ای که در مورد سختی مهم است روش انجام عملیات حرارتی باید استاندارد باشد تا به پوشش آسیب وارد نکند.
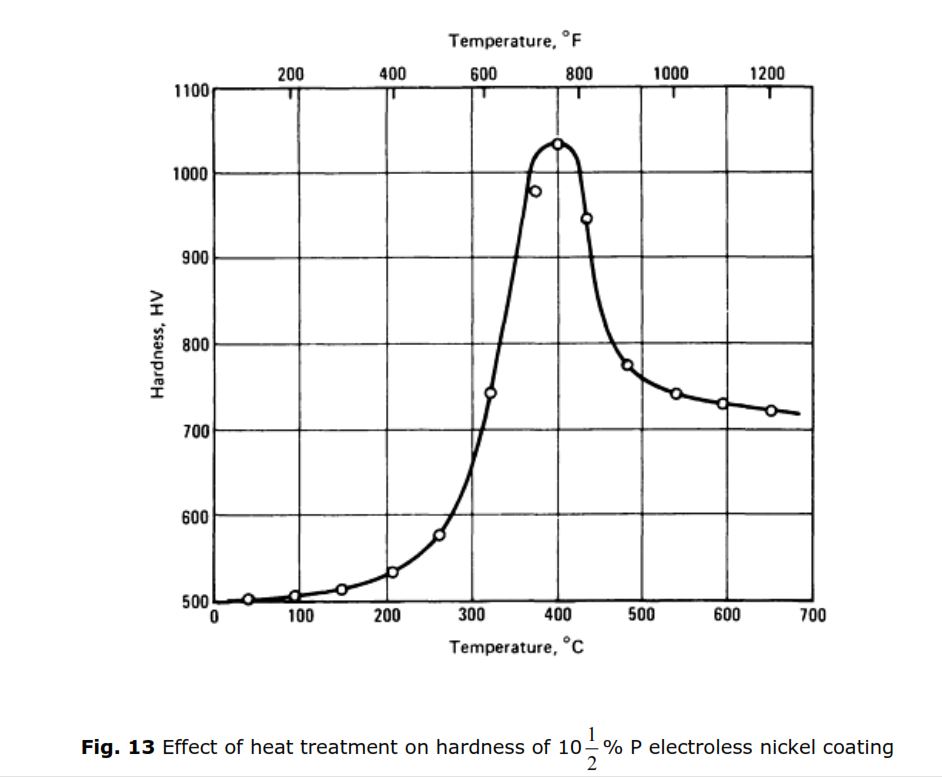
بررسی کارایی پوشش های الکترولس نیکل – فسفر در محیط های خورنده
مقالات تکنیکال بسیار زیادی در مورد مقاومت این پوشش در محیط های خورنده وجود دارد. در صنعت نفت، گاز و پتروشیمی آبکاری الکترولس بسیار محبوب است به دلیل مقاومت این پوشش در مقابل CO2 ، H2S و آب دریا. اگر چه در محیط هایی که نیترات ها و آمونیا ها وجود دارند این پوشش استفاده نمی شود. به منظور ببرسی مقاومت به خوردگی آبکاری الکترولس نیکل (نیکل شیمیایی) تست های زیادی طراحی شده است که در ادامه تعدادی از اینها عنوان می شود.
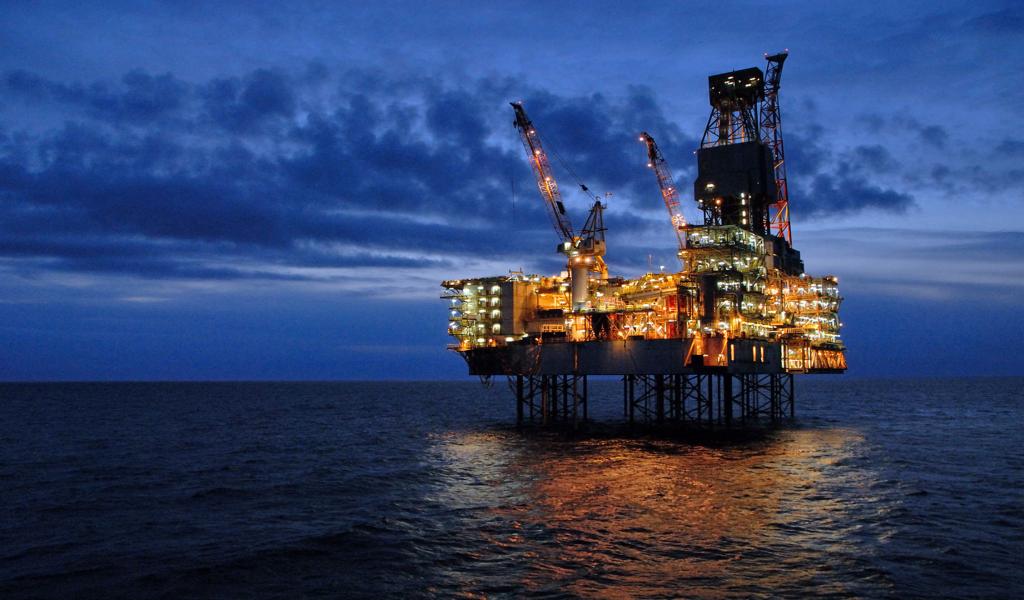
تست آزمایشگاهی
در آزمون آزمایشگاهی باید نمونه در ضخامت های 25، 50 و 90 میکرومتر آبکاری شود این پوشش باید یکنواخت، عاری از تخلخل و ترک و با درصد فسفر 10% باشد.
تست استاتیک
در این آزمایش قطعه داخل یک ظرف شیشه ای مقاوم قرار میگیرد و 200 سی سی محلول خوردنده روی آن ریخته می شود. به گونه ای که داخل محلول غوطه ور شود دما می تواند بین 25 تا 80 درجه سانتی گراد متغییر باشد و زمان نیز بین 120 تا 240 ساعت می باشد. محلول خورنده شامل: کلراید سدیم، کلراید فریک، آمونیا، اسید نیتریک، هیدروکلرید اسید و هیدوکسید سدیم و … می باشد.
تست داینامیک
این آزمایش در یک محفظه استوانه ای از جنس فولاد با حجم 400 سی سی و با پوشش داخلی تفلن قرار میگیرد. این محفظه باید تجهیزاتی داشته باشد که بتوان فشار داخل را تا 4.90 مگاپاسکال افزایش داد و هوای خارج شده باعث هم خوردن محلول خورنده شود. نمونه باید روی یک تخته تفلونی سوار شود و داخل محفظه 350 سی سی از محلول خورنده اضافه شود و بر روی هم زن مغناطیسی با دور 50 دور بر دقیقه قرار گیرد. دما می تواند از 25 تا 80 درجه سانتی گراد و مدت آزمایش بین 120 تا 240 ساعت متغیر است.
تست راکتور فشار بالا
در این تست پوشش الکترولس نیکل داخل راکتور 2 لیتری قرار گرفته فشار باید تا 6.87 مگاپاسکال افزایش یابد و دما بین 25 تا 100 درجه باشد تحت گاز های خورنده H2S و CO2.
تست راکتور رفع فشار لحظه ای
در واقع این تست میزان نفوذپذیری پوشش الکترولس نیکل را نشان می دهد. اگه گاز به زیر پوشش نفوذ کرده باشد با کاهش سریع فشار باعث ایجاد تاول یا پوست شدگی می شود. برای این تست نمونه ها در راکتور 2 لیتری فشار قوی قرار میگیرند که حاوی 200 سی سی آب مقطر اشباع شده با گاز های خورنده است. در این آزمایش راکتور با گاز نیتروژن در فشار 4.9 مگاپاسکال برای 48 ساعت نگه داری میشود. سپس به سرعت فشار به کاهش پیدا میکند تا فشار اتمسفر این کار 3 بار انجام می شود سپس پوشش ارزیابی می شود.
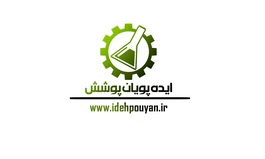
تست میدانی
در تست های میدانی عملکرد پوشش الکترولس نیکل – فسفر در محیط واقعی تست می شود. برای این کار یک لوله 50 سانتی متری را 50 میکرومتر پوشش الکترولس نیکل داده و داخل یک چاه نفت به عمق 1200 متری از بالا قرار می گیرد. در این شرایط نمونه تست در معرض نفت، آب و ترکیبی از گازهای کربن دی اکسید در دمای نزدیک به 70 درجه سانتی گراد قرار دارد و فشار این ناحیه نزدیک به 7.35 مگاپاسکال می باشد. شوری آب نزدیک به 11.2% و PH آن حدود 6.4 می باشد. بعد از 6550 ساعت نمونه خارج می شود. و برای آنالیز به آزمایشگاه فرستاده می شود.
ارزیابی
نمونه ها طبق استاندارد ASTM مورد ارزیابی قرار می گیرند.
هدف پیدا کردن هرگونه نقص، تاول، ناپیوستگی، سوراخ و … در سطح است همچنین بعد از آزمون یون نیکل در محلول های آزمایش نیز بررسی می شود.
نتیجه گیری
براساس مطالب گفته شده و آزمایشات انجام شده می توان نتیجه گیری کرد که
- برای بدست آوردن بهترین نتیجه تمام پارامترها باید در زمان آبکاری و در پایان کنترل شوند.
- در پایان آبکاری باید ضخامت پوشش، یکنواختی پوشش، سختی، چسبندگی، تخلخل، مقاومت به خوردگی و درصد فسفر ارزیابی شود.
- آزمایش ها نشان داد پوشش الکترولس نیکل فسفر یا آبکاری نیکل شیمیایی مقاومت خوبی در محیط هایی با گازهای CO2 و H2S و آب دریا و هیدروکسید سدیم، پتاسیم هیدروکسید و سدیم سولفید دارد.
- مقاومت پوشش الکترولس نیکل در محیط های شامل کلراید فریک، آمونیوم هیدروکسید، نیتریک اسید، اسید کرومیک، هیدروکلرید اسید کمتر است.